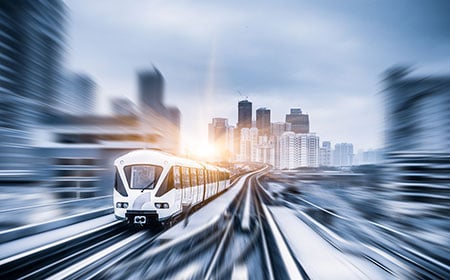
The Biden Administration’s ambition to make 50 percent of all new vehicles sold in the United states electric by 2030 gives a significant boost to the electric vehicle (EV) industry in one of the largest and most competitive markets in the world.
Two pieces of legislation—the $1.2 trillion dollar infrastructure bill passed earlier this year committing $9 billion to nationwide EV infrastructure, and the $3.5 trillion reconciliation package still in Congress—will accelerate growth in service of the transition to a low-carbon economy. In addition, there are provisions for a $7,500 EV tax credit, a $4,500 incentive for union-made EVs assembled in the United States, and funding for EV charging stations. EVs play a critical role in any government policy to enable achieving net zero by 2050, and the global market shift and surge in sales (as well as the associated infrastructure investments) will transform the landscape.
Within this favorable outlook, how can EV manufacturers enhance their competitiveness? To meet demand and fully capitalize on this investment, companies across sectors will need to understand the full lifecycle of each EV, the potential circularity of its components, and how to navigate the expanding domestic manufacturing supply chain to build the connected EV.
Leading through collaboration
The highly integrated nature of the industry means that there are major stakes for the mining, manufacturing, technology, oil and gas, and power sectors. With supply chains already stretched, it’s becoming increasingly clear that this transition will require a whole-systems approach.
The automotive industry is currently characterized by the long-standing manufacturing principle of Just-in-Time (JIT) assembly line manufacturing. Once cutting edge, the current highly automated process is dependent on the completeness and adequate supply of all components. More technology has created an additional dependency on semiconductors, while metal content has decreased and precious metal composition has been limited to integrated circuits and components of higher assemblies. Only recently has a shortage of automobiles materialized, demonstrating the vulnerability of this manufacturing process to critical material shortages.
The connected EV will certainly still be assembled on an automated assembly line, with the automation technology changing and improving to meet the volumes required to meet the administration’s ambitious targets. Radical design changes include new technology to ensure artificial intelligence (AI) and autonomous driving, as well as improved battery technology that is more efficient and utilizes improved materials and methods of extraction to get EV batteries to automotive manufacturers faster. Innovating and developing battery technology for longer distances/wider driving range, larger capacity, and faster recharge time requires further collaboration with battery and EV manufacturers.
In addition, in the oil and gas sector, coordinating with battery manufacturers to understand these improved battery ranges can correctly select retail locations for conversion to charging stations. This in turn leads the power sector to understand where they need to increase capacity to support new charging infrastructure. However, tools like the Evaluation & Development of Regional Infrastructure for Vehicle Electrification (E-DRIVE) demonstrate the complexity in selecting areas for development while advancing strategic and equitable infrastructure investments across the United States.
Circular economy thinking through sustainable design
One crucial strategy companies should consider, underscored by the current materials shortage, is leveraging circularity throughout the EV lifecycle, beginning with sustainable design.
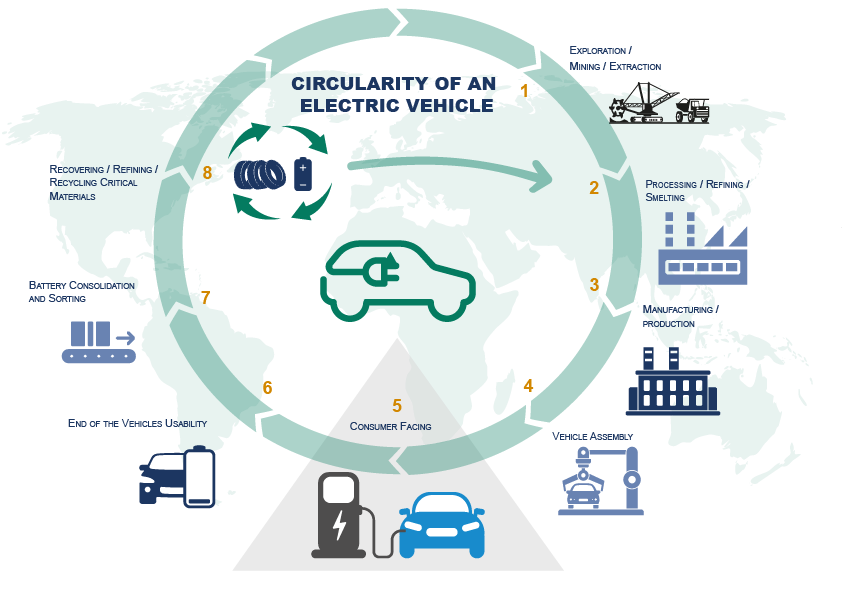
Figure 1. Circularity of an electric vehicle
By streamlining the EV design from the outset with a sustainable end in mind, the main components intentionally are designed to be upgraded, recycled for longevity, and to have precious/recoverable materials easily extracted from them upon return. New EV battery technologies and lifecycle planning are required to advance the storage of power for future use. The non-recyclable components of the EVs can be designed with a proper disposal framework if there is no alternate use for them.
This level of modular circular innovation reduces waste and lowers greenhouse gas emissions, thus creating a new sector of technology focused on the recovery and reuse of EV critical materials and components, and co-creation of manufacturing solutions. By harnessing the value from existing materials, in particular e-waste, billions can be saved in material costs, and the carbon footprint of EVs significantly reduced. Research and development in technology, including self-driving technologies, AI, mapping, remote sensing, 5G infrastructure, and cloud computing, supports EV ambitions and innovations for the next generation of clean technologies.
Meeting demand while improving compliance
Innovators, however, must always look to balance the power of their creativity with the potential consequences of their actions, considering potential regulatory and lifecycle thinking with the consequences for human health and the environment. Building the connected EV will not be enough—the full carbon footprint must be controlled as well, and demand can only be met if companies are able to stay ahead of environmental, social, and corporate governance (ESG) and corporate and social responsibility (CSR) requirements from stakeholders—and not just in their own work.
Reputational and stakeholder risks require extended producer responsibility through the responsibly sourced supply of materials such as key minerals, petroleum-based products (plastics and polymers), and rubber. With accelerated manufacturing practices, manufacturers will have to scale their controls, processes, and Environmental, Health, Safety, and Sustainability (EHSS) practices to ensure the wellbeing of their employees. Barriers that impede production now will only become more critical to successfully navigate as production picks up speed, and in other mature EV markets—such as those in Europe—companies are already expected to miss government-set targets to meet fleet-average CO2 emissions. This will not only lead to a loss in revenue and reputational damage, but also will incur fines from regulators.
With the end in mind, joint and accelerated design, from mine to recovery and reuse, the EV ecosystem can meet the delivery of the volume of EVs by building the connected EV.